Insights into the Evaluation and Certification of Used Heavy Equipment
Discover the intricate process of inspecting, evaluating, and certifying used heavy equipment for sale.
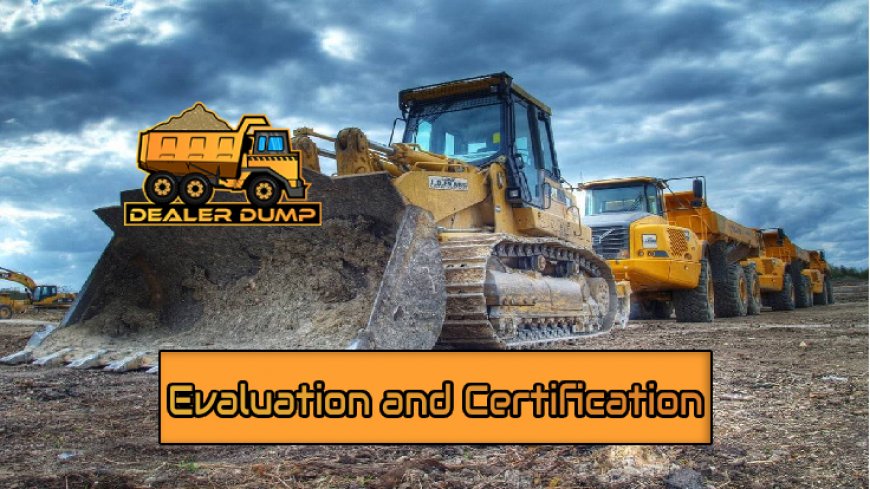
Navigating through the maze of the evaluation and certification of used heavy equipment can be daunting. With so many factors to consider and procedures to follow, some might find themselves overwhelmed. However, understanding this crucial process can not only save you a significant amount of money but also ensure the long-term durability and efficiency of the heavy machinery. This article aims to shed light on the intricate details of inspecting, evaluating, and certifying used heavy equipment for sale in the market.
Preliminary Insights into the Evaluation and Certification of Used Heavy Equipment
When considering the purchase of used heavy equipment, the certification of the machinery's condition is integral. However, this process is layered and requires specific attention to detail. Individual intricacies and processes will be elaborated upon in the following sections of this article.
Table of Contents
- The Inspection Process
- Equipment Evaluation
- The Certification Process
- The Impact of Certification on Used Heavy Equipment
- Decoding Certification Ratings
- Benefits to Stakeholders
- Challenges in Equipment Certification
- Regulatory Insights into Certification of Used Heavy Equipment
The Inspection Process
Before initiating the formal assessment process, an initial inspection of the used heavy equipment is conducted. This first stage digs deep into the machinery to unearth potential issues that may hinder its performance or longevity. Importantly, this process goes beyond surface-level scrutiny and dives into the heart of the equipment.
- Mechanical Check: The mechanical components, including the engine, transmission, and hydraulics, are thoroughly checked.
- Structural Inspection: Machinery structure, including chassis and tracks, are evaluated for any signs of excessive wear or damage.
- Operational Test: The equipment is test-run to gauge its functionality and operational efficiency.
Equipment Evaluation
Following the crucial inspection phase, a comprehensive evaluation of the used heavy equipment is performed. This includes a detailed analysis of machinery health, component wear, and performance standards. In addition, the equipment's maintenance history is also reviewed to predict potential future failures and determine the machine's remaining life expectancy.
The equipment is then graded based on several criteria, including age, operational hours, condition, and maintenance history. The grading process assists in determining its market value and the level of certification it would receive.
Evaluation Reports
Once the evaluation is complete, a report is generated which outlines all the findings. This report is crafted tactfully to accurately represent the condition of the machinery. Moreover, it enables prospective buyers to make an informed choice while purchasing the used equipment.
The Certification Process
Post the equipment evaluation, the official certification takes place. Here, it is important to remember that the focus is not on certifying the mechanical soundness or the structural integrity of the equipment alone. Rather, it extends to verify that the machinery meets all health, safety, and operational regulations. The certification of used heavy equipment thus plays a pivotal role in ensuring the robustness and safety of these massive machines.
The certification is typically granted by an authorized body, ensuring the machinery is safe, reliable, and ready to be put to work. This certification, in turn, validates the market value of the equipment and assures potential buyers of its quality and safety standards.
Remember, a certification is not just a stamp of approval. It's a mark of guaranteed quality that has lasting implications on the usability and maintenance of used heavy machinery.
Note: Although the certification cannot completely eliminate all risks associated with used machinery, it considerably reduces them, bestowing a certain peace of mind to the potential buyers.
The Impact of Certification on Used Heavy Equipment
The influence that certification holds over used heavy equipment is substantial. It acts as an insurance of sorts, offering a guarantee that the equipment has been thoroughly checked and meets all the required safety and operational standards.
Apart from enhancing the market value of the equipment, the certification also boosts buyer confidence. It provides a degree of assurance and transparency, enabling buyers to make informed decisions about their equipment purchase.
Decoding Certification Ratings
As a potential buyer or a seller, understanding what certification ratings stand for can be a game-changer. Generally, the ratings are given based on a combination of factors including machinery condition, operational efficiency, and any potential repairs or restorations needed. To give you a head start, here's what some of the typical ratings might mean:
- 'Like new': This rating indicates that the equipment is in prime condition with very little to no signs of use.
- 'Excellent': Machinery with this rating has minor wear and tear but is still in great functional condition.
- 'Good': Equipment marked as 'good' have visible signs of use but have been maintained well over the years. They are fully operational and safe to use.
- 'Fair': These are machines that have significant usage marks but are still functional. However, they might need some repairs.
- 'Poor': Equipment with this rating might require major repairs or part replacements.
The above ratings, while common, can change depending on the certification body. However, they provide a general benchmark for understanding the condition of the used equipment.
Benefits to Stakeholders
Certification of used heavy equipment isn't just a formality, it brings along a slew of advantages for everyone involved in the deal.
For sellers, it enhances the value of the equipment and boosts the credibility of the sale. For buyers, it provides an assurance of quality, safety, and longevity. For users, it aids in minimizing machine downtime and maintenance expenses.
Benefits for Dealers
For equipment dealers, certification creates a trustworthy reputation in the marketplace. It signals to buyers that the dealer is committed to quality and transparency. This can attract more customers and foster long-lasting business relationships.
Challenges in Equipment Certification
While the credentialing process is indeed beneficial, it's not without its own set of hurdles. The certification process can be time-consuming and expensive. Moreover, non-standardized procedures across different certification bodies can create confusion and discrepancies in interpretation.
However, despite these challenges, the value and security it brings far outweigh the potential drawbacks. Therefore, it is advised to view certification as an investment rather than an unnecessary expense.
Regulatory Insights into Certification of Used Heavy Equipment
In an effort to maintain safety constants and operational efficacy, there are numerous regulatory bodies that oversee the certification process for used heavy equipment. These bodies implement a set of guidelines and regulations to ensure that each piece of certified pre-owned machinery meets the necessary safety and operational criteria.
The rules and regulations may differ from region to region, but they generally aim at establishing a safe and efficient working environment for heavy machinery operators. Therefore, it becomes essential for both sellers and buyers to be well aware of these norms as they look to either sell or purchase used equipment.
Ultimately, investing time and resources into understanding the intricacies of the certification process of used heavy equipment not only ensures safety but also guarantees functional longevity of the machinery.
What's Your Reaction?
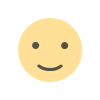
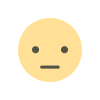
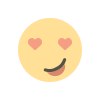
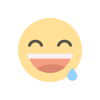

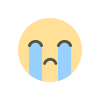
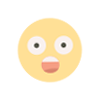